Beam quality in a small engraving machine, or any laser system, is characterized by several parameters that collectively define the laser beam’s performance. These parameters help determine the beam’s focus, divergence, and overall quality.
Some key factors used to characterize beam quality include:
- M² Factor: The M² factor (pronounced M-squared) is a common measure of beam quality. It describes how close the laser beam is to an ideal Gaussian beam. A value of 1 signifies a perfect Gaussian beam, while higher values indicate deviation from the ideal shape.
- Beam Diameter: The beam diameter is the width of the laser beam at a certain distance from the laser aperture. A smaller beam diameter generally indicates better focus and higher beam quality.
- Beam Divergence: Beam divergence measures how much the laser beam spreads out as it travels. Lower divergence values indicate a more collimated (focused) beam, which is desirable for precision engraving or cutting.
- Wavefront Quality: This characterizes how well the laser beam maintains its phase and shape as it propagates. A high-quality wavefront indicates minimal distortion and aberration in the beam.
- Beam Profile: The shape of the beam profile, often Gaussian or near-Gaussian, indicates the intensity distribution across the beam’s cross-section. A well-defined and symmetrical profile is a sign of good beam quality.
- Polarization: The polarization state of the laser beam can impact its quality. A stable and consistent polarization is desirable for certain applications.
Characterizing beam quality involves using specialized instruments like beam profilers, interferometers, or M² measurement systems. These tools analyze various aspects of the laser beam’s properties to quantify its quality based on industry-standard metrics.
In a small engraving machine, beam quality is crucial for achieving precise, detailed, and consistent engraving results. Manufacturers often specify beam quality parameters to ensure the machine’s performance meets the required standards for engraving, cutting, or marking applications.
What are the key components of a small engraving machine system?
A small engraving machine system comprises several key components that work together to perform engraving, marking, or cutting tasks with precision. Here are the fundamental components:
- Laser Source: The laser source emits the laser beam used for engraving. In small engraving machines, this could be a CO2 laser, fiber laser, diode laser, or other types depending on the machine’s specifications.
- Controller/Control Panel: The controller is the interface through which users input designs, adjust settings, and control the engraving process. It houses the software that manages the engraving parameters and coordinates the movement of the machine’s components.
- Motion System: The motion system includes motors, drive systems, small engraving machine and mechanical components that control the movement of the laser head or work surface in X, Y, and sometimes Z axes. It determines the precision and accuracy of the engraving process.
- Optics: Optics consist of lenses and mirrors that manipulate and focus the laser beam onto the workpiece. These components determine the beam’s quality, focus, and accuracy of the engraving.
- Work Surface/Bed: The work surface is where the material to be engraved is placed. It can be a flat table, rotary fixture for cylindrical objects, or specialized surfaces depending on the machine’s capabilities.
- Exhaust System: An exhaust system removes fumes, smoke, and debris generated during the engraving or cutting process, maintaining a clean work environment and ensuring operator safety.
- Cooling System: Some engraving machines incorporate cooling systems, such as air or water cooling, to regulate the temperature of the laser source and other critical components, preventing overheating.
- Safety Features: These include emergency stop buttons, interlocks, and enclosures designed to ensure user safety and prevent accidents during operation.
- Software: Engraving machines rely on software to design, import, and control the engraving process. This software allows users to create or import designs, set parameters, and manage the engraving operation.
- Power Supply: The power supply provides electrical power to the various components of the engraving machine, including the laser source, motion system, and control electronics.
These components work cohesively to enable the engraving machine to perform its intended functions accurately, efficiently, and safely. The integration and proper functioning of each component are crucial for achieving high-quality and consistent engraving results.
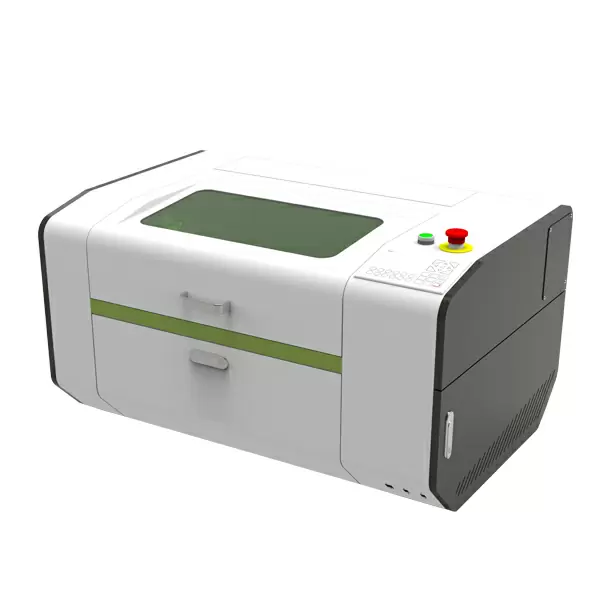