Hydraulic motors are mechanical devices that convert hydraulic pressure and flow into torque and rotational motion. They are commonly used in industrial machinery, construction equipment, and transportation vehicles.
Here is an overview of hydraulic motors, equipment, and repair:
Hydraulic Motors:
Hydraulic motors can be classified into two main types: rotary and linear. Rotary hydraulic motors convert hydraulic pressure and flow into rotary motion, while linear hydraulic motors convert hydraulic pressure and flow into linear motion.
There are several types of hydraulic motors, including gear, vane, piston, and radial piston motors. Each type has its unique features, advantages, and applications.
Hydraulic Equipment:
Hydraulic equipment is used to generate, control, and transmit hydraulic power. It includes hydraulic pumps, valves, cylinders, and hoses. Hydraulic equipment is widely used in various industries, including construction, manufacturing, and transportation.
Hydraulic Repair:
Hydraulic repair is essential to keep industrial machinery and equipment running smoothly. Hydraulic components may wear out, leak, or malfunction over time due to wear and tear, contamination, or other factors.
Hydraulic repair involves diagnosing the problem, repairing or replacing damaged parts, and testing the system to ensure it is functioning correctly. It is essential to work with a trained and experienced hydraulic repair technician to ensure the repair work is done correctly and safely.
In summary, hydraulic motors and equipment play a crucial role in various industries, and hydraulic repair is essential to maintain their functionality. Proper maintenance and repair of hydraulic systems can extend their lifespan, improve efficiency, and reduce downtime and repair costs.
How often should hydraulic systems be inspected and maintained?
The frequency of hydraulic system inspections and maintenance depends on several factors, including the type of equipment, the operating conditions, and the manufacturer’s recommendations. In general, h1b110 danfoss suppliers hydraulic systems should be inspected and maintained regularly to ensure their optimal performance and longevity.
Here are some general guidelines for hydraulic system inspections and maintenance:
Regular Inspections: Regular visual inspections of hydraulic systems should be performed daily or weekly, depending on the equipment’s usage. Inspections should include checking for leaks, loose connections, and any signs of wear or damage.
Fluid Analysis: Fluid analysis is an essential part of hydraulic system maintenance. It helps to identify any contaminants, such as water, dirt, or metal particles, that may be present in the system, which can cause damage and reduce efficiency. Fluid analysis should be performed at least once a year, or more frequently if the equipment operates in harsh conditions.
Filter Replacement: Hydraulic filters should be replaced regularly to prevent contaminants from entering the system. The frequency of filter replacement depends on the equipment’s usage, environment, and the type of filter used. A general rule of thumb is to replace filters every 500 hours of operation.
Component Maintenance: Hydraulic components, such as pumps, valves, and cylinders, should be inspected and maintained regularly to ensure their optimal performance. The frequency of component maintenance depends on the equipment’s usage and manufacturer’s recommendations.
Professional Maintenance: It is recommended to have a professional hydraulic technician perform regular maintenance and repairs on hydraulic systems. A professional technician can identify potential problems before they become major issues, ensuring the system operates efficiently and safely.
In summary, regular inspections, fluid analysis, filter replacement, and component maintenance are essential to keep hydraulic systems running efficiently and safely. The frequency of inspections and maintenance depends on the equipment’s usage and operating conditions, and it is essential to follow the manufacturer’s recommendations and consult with a professional hydraulic technician when necessary.
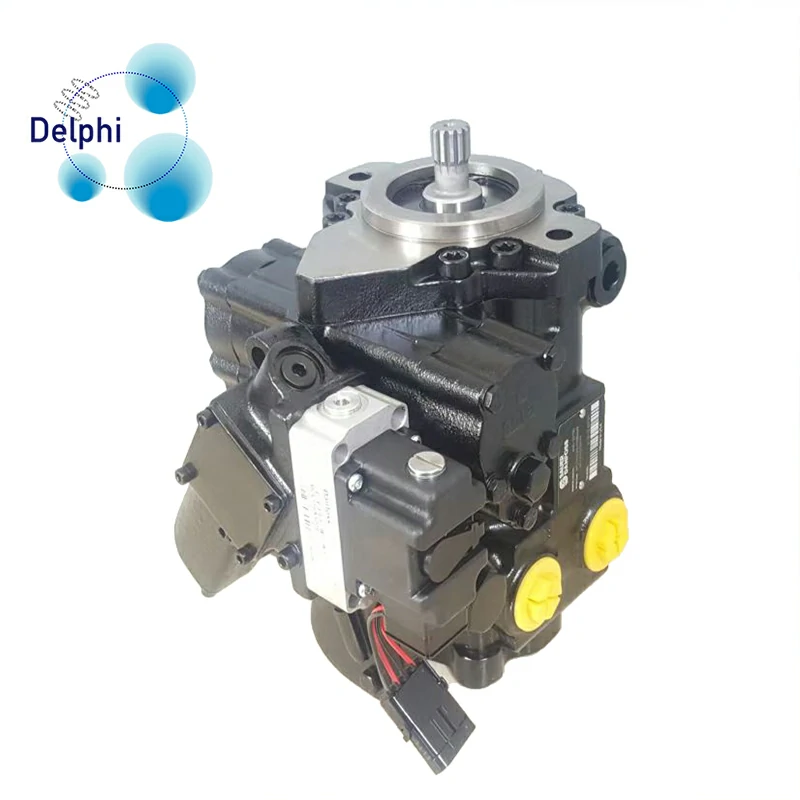