A black pipe compression fitting is a type of plumbing component used to create secure and leak-free connections in plumbing and piping systems. These fittings are designed to join two sections of pipe together, typically made of black steel or other compatible materials, while ensuring a tight and reliable connection.
Here’s a detailed explanation of what a black pipe compression fitting is and how it functions:
Black Pipe Compression Fitting:
- A black pipe compression fitting consists of several components, including a compression nut, a compression ring (also known as a ferrule), and the fitting body. The fitting body is threaded and has an interior cavity where the compression ring and pipe are inserted. The compression nut is threaded onto the fitting body and compresses the ring and pipe to create a seal.
Function in Plumbing and Piping Systems:
- The primary function of a black pipe compression fitting is to join two sections of pipe together while ensuring a tight and leak-free connection. It is particularly useful in applications where threaded connections, welding, or soldering are not desirable or practical.
- The compression fitting works by compressing the compression ring against the pipe when the compression nut is tightened. This compression creates a watertight or airtight seal, preventing fluid or gas leaks from the joint.
- Black pipe compression fittings are commonly used in water supply systems, gas lines, HVAC systems, and industrial applications. They are versatile and can be used with a variety of pipe materials, including black steel, black pipe compression fitting copper, and plastic.
- One of the advantages of compression fittings is that they are relatively easy to install, making them a popular choice for DIY projects and professional installations. They do not require soldering, welding, or special tools.
- To install a black pipe compression fitting, the pipe is first cut to the desired length and then inserted into the fitting body. The compression ring is slid over the pipe and positioned against the fitting body. The compression nut is threaded onto the fitting body and tightened, which compresses the ring against the pipe, creating a secure and leak-free connection.
- Properly installed black pipe compression fittings offer a reliable and long-lasting solution for connecting pipes in plumbing and piping systems, provided they are used within their pressure and temperature ratings and are correctly tightened.
In summary, a black pipe compression fitting is a plumbing component designed to create secure and leak-free connections by compressing a compression ring against a pipe. Its function is essential in joining pipe sections together in plumbing, HVAC, and industrial systems while ensuring a watertight or airtight seal. These fittings are versatile and practical alternatives to other connection methods and are widely used in various applications.
What safety measures should be taken when working with black pipe compression fittings, particularly in high-pressure or critical applications?
Working with black pipe compression fittings, especially in high-pressure or critical applications, requires strict adherence to safety measures to ensure the integrity of the system and the safety of personnel.
Here are important safety measures to consider:
- Proper Material Selection: Ensure that the materials used for black pipe compression fittings are compatible with the specific fluid or gas being transported. Material compatibility is crucial to prevent corrosion, contamination, or degradation.
- Pressure Ratings: Use compression fittings with pressure ratings that match the requirements of the application. Using fittings with lower pressure ratings in high-pressure systems can lead to system failures. Check that the fittings are properly marked with their pressure ratings.
- Manufacturer Recommendations: Follow the manufacturer’s guidelines for installation, torque specifications, and recommended procedures. Different manufacturers may have specific requirements for their fittings.
- Pipe Preparation: Properly prepare the pipe ends before installing compression fittings. Ensure that the pipe is clean, free from burrs, and cut to the correct length. Deburr the pipe edges to prevent damage to the O-rings or ferrules.
- O-Ring Inspection: Inspect the O-rings or ferrules for signs of damage or wear before installation. Damaged O-rings should be replaced to maintain the integrity of the seal.
- Proper Installation: Ensure that compression fittings are correctly installed. Over-tightening can damage the threads and O-rings, while under-tightening can lead to leaks. Follow the manufacturer’s torque specifications and installation guidelines.
- Leak Detection: After installation or maintenance, conduct a leak detection test to check for any potential leaks. Use a leak detection solution to inspect threaded connections for bubbles, indicating a leak. Address any leaks promptly.
- Hydraulic Testing: In high-pressure applications, consider conducting a hydraulic test on the system to ensure that it can withstand the specified pressure without issues. Follow safety protocols during testing, and have a clear plan in case of system failure.
- Regular Inspection: Periodically inspect the system for signs of wear, corrosion, or damage. Address any issues promptly to prevent system failures. Include compression fittings in your routine inspection process.
- Isolation and Lockout/Tagout: Before working on the system, isolate it from other equipment and perform lockout/tagout procedures to ensure that no unexpected pressure or fluid release occurs during maintenance.
- Safety Regulations: Comply with industry and local safety regulations, as well as any specific requirements for the application. Follow established safety standards to ensure the protection of both personnel and the system.
- Qualified Personnel: In high-pressure or critical applications, consider using qualified and experienced personnel who are trained to work with such systems. Proper training and expertise are essential to avoid accidents.
- Emergency Response: Establish and communicate emergency response procedures for potential incidents, such as leaks or sudden pressure releases. Ensure that all workers are familiar with these procedures and that emergency equipment is readily available.
It’s essential to note that safety measures may vary based on the specific application, the type of fluid or gas being transported, and the pressure levels involved. Always consult industry standards, safety guidelines, and the manufacturer’s recommendations when working with black pipe compression fittings in high-pressure or critical applications.
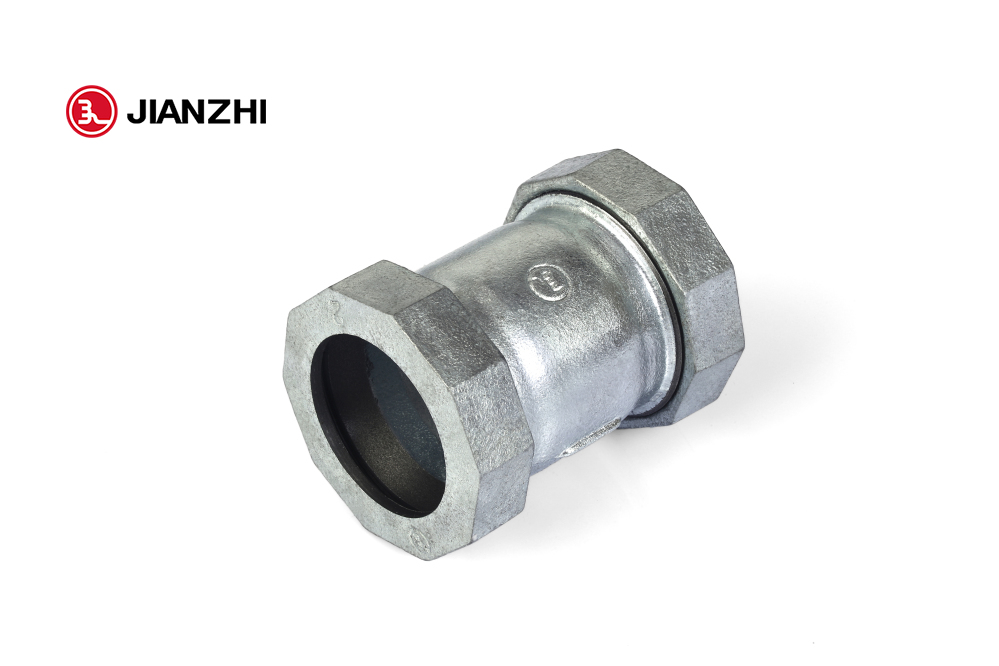